Dünyanın enerji kaynaklarının sınırlı olmasına rağmen, günümüzde toplumların refah seviyelerinin yükselmesine paralel olarak enerji gereksinimleri sürekli artmaktadır. Artan enerji talebini karşılamak üzere bazı alternatif enerji kaynaklarını kullanmak teorik olarak mümkün olsa da günümüz teknolojisi ile bunların büyük ölçekli uygulanması pratik değildir. Bu sebeple eldeki mevcut enerji kaynaklarının en verimli bir şekilde kullanılması gereklidir.
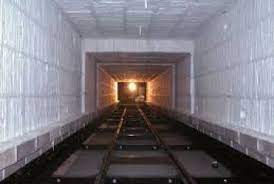
Kullandığımız birçok malzemenin üretim sürecinde bir çeşit ısıl işlem mevcut olduğundan, toplam enerji tüketiminde fırınlar büyük bir paya sahiptir. Fırınların ısıl verimini artırmak üzere tasarlanmış ve kullanılmakta olan bazı sistemler mevcuttur. Bunların başında da atık ısı geri kazanım sistemleri gelmektedir. Bu sistemlerde genel olarak egzoz gazları kullanılarak taze yanma havası veya ısıtılacak kütle ön ısıtmaya tabii tutulmaktadır. Ancak bu sistemlerin orta ve küçük kapasiteli fırınlara uygulanması ekonomik olmamaktadır. Bu sebeple yanma ürünlerinin enerjisinden mümkün olduğunca fırın içerisinde faydalanılması yoluna gidilmelidir. Bu da imalat aşamasında fırınlara yapılan iç ve dış yalıtımlar ile mümkün olmaktadır. Yine enerjinin faz dönüşümünün olduğu, tüm makine ve araçlarda bu ve buna benzer geri kazanım yalıtımları düşünülmesi kaçınılmazdır.
Yüksek sıcaklıkların (800¡C ve üzeri) söz konusu olduğu ısı ve ses yalıtımlarında artık seramik fiberleri oldukça yüksek bir kullanım alanı bulmaktadır. Önceleri camsı fiberler oldukça düşük sıcaklık olan 1000¡C'a kadar kullanılırdı. Petrol krizi nedeniyle, kesikli çalışan fırınlara, bohçalama, yalıtımlara giderek, artan oranlarda seramik fiber uygulanmaya başlandı. Bunun sonucu olarak ısı tasarrufu, ekipmanlarda da ağırlık azalması sağlandı. Geniş bir uygulama alanında, seramik fiber uygulamaları popüler olmaya devam etmektedir. Seramik fiberlerin yaklaşık % 62'si çelik endüstrisinde kullanılmaktadır. Kristal seramik fiber, endüstride camsı seramik fiber kadar uygulama alanı bulmaktadır.

Camsı fiber seramiklerde yüksek sıcaklıkta küçülme ve hasar meydana gelir. Kristal seramik fiber daha yavaş tane büyümesi gösterir ve camsı seramik fiberlerden çok daha az pişme küçülmesi ve hasar gösterir. Seramik fiberler düşük ısıl iletkenlik, düşük ısı depolama, hafiflik, kolay ve çabuk yerleştirme ve tamir, termal şoklara dayanıklılık gibi anahtar faktörler nedeniyle ticari malzemelerden farklı olarak dikkat çekerler.
Seramik fiberler ilk defa 1950 yılında Amerika'da uzay araştırmalarında kullanılmak üzere geliştirildi. Üretim teknolojisi sıvı seramiği, merkezkaç kuvvet etkisinde ince deliklerden püskürtmekten ibarettir. Bileşimleri, ergime sıcaklıkları, maksimum kullanım sıcaklıkları birbirinden çok farklı fiberler vardır; fakat seramik fiber denildiği zaman, maksimum 1260¡C olan fiberler akla gelmektedir. Camyünü, kayayünü vb. fiberler bu grupta yer almazlar. Kristal veya mikro kristal diye adlandırılan ve maksimum kullanım sıcaklığı, göreceli olarak daha yüksek olan fiberlerin kullanımının daha hızlı artması beklenmektedir. Seramik fiberlerin yoğunluğu, yalıtım ateş tuğlasının yaklaşık üçte biridir. Fiber yerine, yoğunluğu, fiberlerin yaklaşık 3 katı daha ağır olan yalıtım ateş tuğlası kullanılsaydı, toplam refrakter tuğla tüketimindeki payı yüzde 25 olurdu. Bu oran fiberlerin ne kadar büyük öneme sahip olduğunu göstermektedir. 1980'den sonra alümina fiberler, zirkonya fiberlere üstünlük sağlamıştır. Fakat kimyasal etkilere dayanıklılık söz konusu olduğunda zirkonya hala üstündür. 1970’li yılların başında petrol fiyatlarının, yüzde 100'ün üzerinde artması tüm dünyada ve tüm enerji kullanan sektörlerde tasarruf tedbirleri alınmasına neden oldu. Bu sorun, 1950’de keşfedilmiş ama pek uygulama alanı bulamamış fiberlerin çok hızlı gelişmesine ve yaygınlaşmasına yol açtı. Fakat ülkemizde 1987’ye kadar istenilen düzeye gelememiştir. Pazarlayan kuruluşların yetkilileri bile ürünlerinin özelliklerini tanıtamamaktadırlar. 1990’lar sonrasında, yeni yapılan fırınlarda bir ton sıvı çelik üretmek için harcanan refrakter miktarı 90 kilogramdan 8 kilograma düşmüştür. Kullanılmakta olan yüzde 10 seramik fiber yerine yalıtım ateş tuğlası kullanılsaydı refrakter tüketimindeki payı yüzde 25 olacaktı. Yüzde 15’lik düşüşte, seramik fiberlerin payı vardır.
Whiskerlerin mukavemeti ve elastiklik modülü, fiber çapına bağlı olarak Grafik l’de görüldüğü gibi değişmektedir. Çapın küçülmesine bağlı olarak mukavemetin bu kadar artması, tek kristal olması, mükemmel yapısı ve yüzey yapısı ile açıklanabilir. Fakat dis-lokasyonların kilitlenmesinin de büyük rolü vardır. Çap küçük olduğu için kayma sadece yüzeye yakın yerlerde olur.
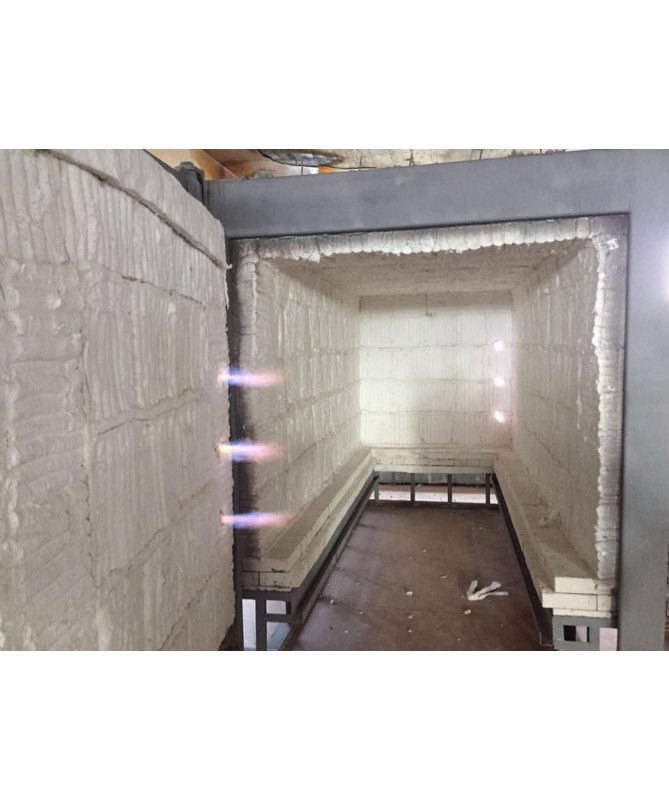
2. SERAMİK FİBERLERİN ÖZELLİKLERİ
Fiberler 1950’de keşfedilmesine rağmen 70’li yıllardaki enerji krizine kadar pek gelişme gösterememiştir. 1970 öncesi zirkonya fiber kullanılırdı ve çok pahalıydı. Yüksek sıcaklık dayanımı ve kimyasal maddelere dayancı çok iyiydi. Enerji kriziyle birlikte seramik fiberler geliştirildi.
Alüminosilikat fiberler ya tabiatta bulunan saf kaolinden ya da saf alümina ve silika karışımlarından üretilir. Yüzde 80 ve yüzde 95 alümina içeren türlerin üretiminde Bayer prosesi ile üretilmiş alümina kullanılır. 1980 öncesi 3 tip fiber üretilirdi. Şimdi yüzde 80 Al2O3+% 20SiC>2 bileşiminde kristal seramik fiber kullanılmaktadır ve maksimum kullanım sıcaklığı 1700-1750 ¡C arasında değişir. Yoğunluğu 481 kg/m3'tür.
1260 ¡C'lık fiberlerin tipik özellikleri fiber çapı (ortalama) 2.5-3 ğm fiber boyu (maksimum) 250 mm. Fiber boyu (ortalama) 100 mm, özgül ağırlık (ASTM 135) 2.56 yüzde 80 alüminalı fiber, yüzde 95'likten sonra geliştirilmiştir. Dolayısıyla yeni geliştirilen bu fiberin, eskisinin yerini almış olması olasıdır. Alümina oranı yüzde 15 daha düşük olduğu için fiyat yönünden de avantajlı olması söz konusudur. Bugün satılmakta olan fiberler, camsı ve kristal olmak üzere 3 gruba ayrılmaktadır. Camsı fiberler yüzde 45-56 Al2O3, kristal fiberler yüzde 74-94 Al2O3 içerirler. Geri kalanı ise silikadır. Bu iki bileşenin dışındaki yabancı maddeler çok düşük orandadır. Camsı seramik fiberlerde Al2O3/SiO2 oranı yaklaşık yarı yarıyadır ve maksimum kullanım sıcaklığı 1260-1300¡C'dir. 1400¡C'a dayanan camsı fiberlerde Al2O3 yüzde 60, SiO2 yüzde 40'tır. Camsı fiberlere Cr2O3 katarak, maksimum kullanım sıcaklığı artırılabilir. Camsı seramikler, yüksek sıcaklıkta büzülme gösterirler. Mullit veya krista-balit kristalizasyonu gerçekleşir. Cr2O3, bunu önler. Kristal seramik fiberlerde alümina oranı yüzde 70’in üzerindedir. Bunlarda çok yavaş tane büyümesi olur.
Yoğunluğu düşük olan seramik fiberler düşük sıcaklıklarda etkin yalıtım sağlarlar. Fakat sıcaklık yükseldiği zaman ısı iletimi mutlak sıcaklığın (Kelvin) dördüncü kuvveti ile, yani radyasyonla gerçekleştirdiği için boşluk hacmiyle orantılı artar ve gözenek çapı dağılımına da bağlıdır.
Isıl iletkenlik, 48 kg/m3 yoğunluklu seramik fiberde 400-600 arasında yaklaşık yüzde 54 artarken, 160 kg/m3 yoğunlukluda yüzde 38 artmaktadır. 160 kg/m3 yoğunluklu fiberin 1200 ¡C’daki ısıl iletkenliği, 400 ¡C’daki iletkenliğin 4 katıdır. Bu nedenlerle, kullanım sıcaklığı arttıkça, seramik fiber malzemenin yoğunluğunu artırmak gerekmektedir. Grafik 3'te görüldüğü gibi, diğer fiber malzemelerin en yüksek kullanım sıcaklığı düşüktür ve seramik fiberlerle rekabet şansı yoktur. Mineral yüne bağlamakla ve organik bağlayıcı katılarak üretilen kompozit seramikler 760 ¡C’a kadar kullanılabilmektedir. Seramik fiberler yüksek alüminalı çimento ile karıştırılarak da kullanılabilmektedir. Bu tip duvarlarda, ısınma sırasında meydana gelen termal gerinimler incelenmiştir.
Seramik fiberler, ısı yalıtımında gösterdiği bu üstün performansın yanı sıra sahip olduğu fiber yapı sayesinde iyi bir ses yalıtım malzemesi olarak da sanayiinin çeşitli kollarında kullanılmaktadır. Ayrıca yüksek sıcaklıkta filtrasyon gerektiren ortamlarda, yüksek sıcaklıklarda yüksek yüzey sürtünmesi gerektiren yerlerde, yine yüksek sıcaklıklarda vibrasyona dayanıklı malzeme olarak ve yangın yalıtımında kullanımı son yıllarda oldukça artmıştır.
3. SERAMİK FİBERLERİN KULLANIM YERLERİ
Hızlı ısınan fırınlarda genellikle MoSi2 ısıtıcı ve seramik fiber kullanılmaktadır. MoSi2 ile çalışan seramik fırınlarında hız ayarı için sınır değer konulmamıştır. MoSİ2 ısıtıcılı küçük bir seramik fiber fırında, 2 dakikada 1000¡C’ye, 10 dakikada 1500¡C’ye çıkılmıştır. Aynı fırının kapağı açılarak 3 dakikada 800¡C’a soğutulabilmektedir. Hızlı ısınma ve soğuma kesikli çalışan kamara tipi fırınlarda üretim kapasitesini artırır. Kapasite artışı, fırın ilk yatırım maliyetini düşürücü etki yapar. Aynı zamanda üretilen parça başına ısı enerjisi düşer. Enerji krizinden sonra seramik fiberler, kesikli çalışan fırınlara, potalara ve benzerlerine uygulanmaya başlandı. Enerji tasarrufu yanında, fırın ve potalarda ağırlık azalmasına da neden oldu. Ardından kristal fiberler üretilmeye başlandı. Kristal fiberlerin kullanım sıcaklığı camsı fiberlere göre daha yüksektir.
Fırın, kapasitesinin artmasına veya azalmasına ayak uydurabilmelidir. Planlı kapatmalarda ısı kaybının en az olması hedeflenmektedir. Potalarda yalıtım, pota ağırlıklarının azalmasına neden olmaktadır. Fiber temel olarak çelik endüstrisi, kimya endüstrisi ve refrakter endüstrisinde kullanılmaktadır. 1700¡C'a kadar çıkan fırınlarda genellikle metalik tozların veya refrakter, yapısal seramik ve elektronik uygulamalarda tozların sinterlenmesinde ve kristal büyütme işlemlerinde kullanılırlar. Seramik fiberli hızlı ısınan fırınlar, yüksek sıcaklıkta kısa süreli pişirilecek olan bu uygulamalarda son derece yararlıdır. Hızlı ısınıp hızlı soğurlar. Genellikle laboratuvar tipi fırınlardır. Gaz veya sıvı yakıtla ısıtılan fırınlarda, fırın iç yüzeyinde gaz hızı 10Ğ15 m/s'yi geçerse, battaniye şeklinde değil, plaka şeklinde fiber kullanılmalıdır. Gaz hızı 100 m/s'yi geçerse, dar kesitli fiber plakaların üst üste konmasıyla duvar oluşturulur. Camyünü ve kayayününün maksimum kullanım sıcaklıkları 1000¡C'ın altında olduğu için, bu sıcaklığın üzerindeki sıcaklıklarda seramik fiber kullanılır. Buhar ve gaz türbinlerinde, baca yalıtımlarında seramik fiberler kullanılır. Asbest kanserojen olduğu halde, seramik fiberler kanserojen değildir.
Seramik fiberlerin kullanım alanını sınırlayan çok az faktör vardır. Bunlardan en önemlisi mekanik zorlamalara dayanıksızdırlar. İkinci önemli faktör hidrojen, yüksek sıcaklıkta SiC'yi redükleyebileceği için kullanılmaz. Üçüncü faktör, seramik fiberlerin yüksek sıcaklıkta iletkenliği artar. Bunlara seramik fiberlerin avantajlarını azaltan faktörler diye bakabiliriz. Mekanik zorlama söz konusu ise 1000¡C altında, yerine perlitli dökülebilir refrakter kullanabiliriz. Fiberler ayrıca sıvı ile temas olan uygulamalarda kullanılamazlar.
Seramik fiberlerin etkin olarak kullanıldığı yerlerden biri de, tünel ve kamara tipi fırınların arabalarıdır. Eski arabalarda, pişecek seramiklerin oturduğu en alt plakanın altına seramik fiber konulmaktadır. Bu, ısı transferini ve depolanan enerjiyi azaltır. Yeni tünel fırın arabaları, seramik fiber kullanılacağı göz önüne alınarak dizayn edildiği için, yukarıdaki faydaları artırır, ilaveten fırın arabalarının hafiflemesine de yardım eder. Refrakter ömrü artar, çünkü refrakter termal şoklara maruz kalmaz. Tekerlek sıcaklıkları düşer. Fırın kesitinde sıcaklık dağılımı daha homojen hale geldiği için ürün kalitesi iyileşir. Başka bir deyişle, fırının değişik bölgelerinden geçerek pişen seramiklerin, özellikle sırlı seramiklerin rengi birbirine çok yakın olur. Fırın arabaları fazla ısı depolanmadığından pişirme hızını artırılabilir.
Çelik ısıtma tünel fırınlarında 1100 ¡C'ın altında bir sıcaklığa kadar ısınan bölgelerde camsı; 1100-1200 ¡C arasında ısınan bölgelerde cam-kristal fiberler karışık; 1200 ¡C'ın üzerindeki uygulamalarda kristal fiber kullanılmaktadır. Bazı uygulama örnekleri: 1140¡C'a çıkan, gazla çalışan 8 bisküvi fırınında 50 mm kalınlığında fiber yalıtımı ile yüzde 18 yakıt tasarrufu ve her periyotta 6 saatlik zaman kazancı sağlanmıştır. 1160¡C'ye çıkan ve gazla çalışan bisküvi fırınında ise 50 mm kalınlığında fiber yalıtımıyla yüzde 28 yakıt tasarrufu elde edilmiş ve üretim kapasitesi iki katına çıkmıştır. 1450¡C’lik gazla çalışan porselen fırınında 50 mm'lik alümina fiber yalıtımıyla yüzde 20 yakıt tasarrufu sağlanmış, pişme zamanı 30 saatten 21 saate düşmüştür. Tüm üretim kapasitesi yaklaşık yüzde 30 artmıştır. Bir porselen firması 400 mm kalınlığındaki dökülebilir refrakter duvarı yıkıp 140 mm kalınlığında fiber duvar yapmıştır. Bir buçuk günde pişirme sıcaklığına çıkan fırın yeni uygulamayla 45 dakikada aynı sıcaklığa çıkar hale gelmiştir. Bu durumda ayda 2000 dolar yakıt tasarrufu sağlanmıştır. İşgücü, işlem ve kontrol maliyetlerindeki azalma bunun dışındadır. Ateş tuğlasından yapılmış kamara fırın kapısı, fiberden yapıldığı zaman, ağırlık 300 kilogramdan 25 kilograma düşmüştür. Ayrıca gaz sızdırmazlığı iyileşmiştir. Çimento endüstrisinde döner fırının çevresine sadece 2 katlı yoğun fiber uygulayarak hem ısıl hem de mekanik verim artırılmaktadır. Göreceli olarak ince olan fiber uygulaması bile döner fırın yüzey sıcaklığını 35 ¡C’a düşürür. Bütün uygulamalarda, seramik fibere yapılan yatırım, kendini birkaç ayda amorti eder. Fiberlerin astarlama metotları konusunda tüm makalelerde farklı farklı yöntemlerden bahsedilmektedir. Sınıflamalar birbirinden çok farklıdır.
Önümüzdeki sayıda "Refrakter Üzerine Battaniye Uygulaması", "Fiber Blok Uygulaması", "Kağıt Astarlama", "Yığın Astarlama", "Seramik Fiber Duvar", "Otomotiv", "Uzay ve Uçak Endüstrisi" ve "Seramik Fiberlerin Kullanım Avantajları" konularını ele alacağız.
KAYNAKLAR
1. Yaman, C. "Seramik Fiberlerin Özellikleri ve Isı Tasarrufu
Amacıyla Kullanılması"
4. Seramik Teknik Kongresi, Kimya Mühendisleri Odası, 459Ğ465 (1990).
2. Arcasoy, A. Seramik Elyaflı
Yalıtım Malzemelerinin Seramik Fırınlarındaki Enerji Tasarrufu Bildiriler Kitabı, Seramik Teknik Kongresi, Kimya Mühendisleri Odası, 430-435, Ağustos 1987.
3. Teknotherm Kataloğu, Seramik Elyaf
4. Yaman, C. 1998 "Seramik
Fiberlerin Özellikleri ve
Kullanım Alanları"
Metal Dünyası Ocak 1998,
5. Thermal Ceramic Kataloğu
Alıntıdır:TEKNİK MAKALE
68. Sayı (Eylul-Ekim 2007)
Ömer KARA Sanifoam Sünger San. ve Tic A. Ş. Genel Müdür Yrd. (Üretim)
Comments